Автор: Анна Фединцева, ООО «НПП ПРОТОН», главный технолог, fam@npp-proton.ru
В ныне сложившейся ситуации в нашей стране многие промышленные предприятия вынуждены модернизировать своё производство и ускорять темпы выпуска продукции в несколько раз. Данная ситуация не обошла стороной и такую консервативную отрасль как ВПК. К нам обратилось одно из предприятий, которым потребовалась срочная модернизация производства кабельных жгутов. Как мы понимаем, на таких предприятиях существуют определенные проблемы в связи с тем, что конструкторская документация (КД) и технология изготовления жгутов были разработаны несколько десятилетий назад. Но новые реалии диктуют нам новые условия и требования...
Самое главное требование, которое выдвинул заказчик – это ускорить выпуск кабельных жгутов как минимум в два раза. Изучив рынок оборудования, инструментов и новых материалов, которые ничем не уступают, а в чем-то даже превосходят материалы прошлых лет, мы взялись за решение этой сложной задачи и пересмотрели все этапы производства, начиная от склада и заканчивая электроконтролем.
Итак, начнем. Участок материалов и покупных комплектующих изделий.
Проблема, которая существует на данном участке – провода поступают от поставщиков в бухтах, либо на катушках большого диаметра. При перемотке провода с бухты на катушку провод начинает запутываться, скручиваться и заламываться, а иногда даже образуются узелки. А провода, намотанные на катушки большого диаметра иногда невозможно перемещать вручную из-за их большой массы, либо такие катушки невозможно установить на станок для резки проводов (посадочное место рассчитано под катушки меньшего диаметра). Поэтому они подвергаются перемотке на катушки меньшего диаметра. Как правило, такие работы производят в ручном режиме, на что уходит драгоценное время.
Что предложили мы?
1. Станок для размотки бухт проводов. С помощью этого станка перематываются провода с бухт на катушки нужного нам диаметра в автоматическом режиме.
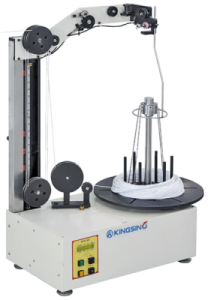
2. Станок для намотки провода на катушки. С помощью станка возможна перемотка провода с катушек большего диаметра на катушки меньшего диаметра, а также упорядочение рядности намотки провода (виток к витку). Все это опять в автоматическом режиме.
Тем самым мы экономим время на перемотку и получаем готовые намотанные катушки, с которыми могут работать как люди, так и оборудование, а также при хранении таких катушек они занимают меньше места и могут аккуратно храниться на полках.
Следующий - Заготовительный участок.
Основные проблемы данного участка:
1. Нарезка проводов на каждый жгут является важной и трудоемкой работой электромонтажника, особенно если жгут более 2-3 метров в длину и имеет несколько разъемов на концах. При таком большом количестве проводов не сложно допустить ошибку. Ведь необходимо собрать жгут по КД. А сколько времени уходит на обработку концов проводов – обрезать плетенку (при наличии), снять изоляцию на необходимую длину, а если в контакт паяется несколько проводов, то их необходимо скрутить вместе. И завершающий этап – обработать концы проводов флюсом и облудить припоем. На большинстве наших предприятий ВПК все это делается вручную, крайне редко где встречаются хотя бы автоматические линии для резки проводов. На этом этапе мы опять теряем драгоценное время.
2. Далее провода раскладываются на плазе опять же в ручном режиме. Хорошо, если такие плазы есть на предприятии, а ведь у некоторых все это делается на обычном рабочем месте или на полу, что очень неудобно и отнимает много времени на подготовку. И опять здесь вмешивается человеческий фактор – по ошибке мы можем взять провод не той марки или сечения.
3. И еще одна проблема – основная – это прозвонка (поиск) каждого провода перед каждым контактом разъема при монтаже, что занимает не один час, особенно если жгут трудоемкий.
Наши решения:
1. Со склада перемотанные катушки с проводами поступают на участок для мерной резки. Но как мы с Вами понимаем у каждого предприятия очень большая номенклатура проводов. И для того, чтобы не занимать много места станками или приспособлениями для каждой отдельной катушки в современном мире существует система подачи провода, на которую устанавливается одновременно 8 катушек с проводами разного сечения, а также данная система помогает разматывать провод с катушки и при необходимости отматывать его обратно на катушку. Скорость подачи провода регулируется и настраивается для каждой катушки в отдельности.
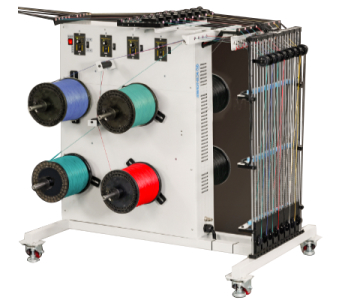
2. После мерной резки необходимо подготовить концы проводов к монтажу (пайке) в разъемы. И тут нам на помощь придет Автоматическая линия для обработки проводов, специально спроектированная под этот проект отечественным предприятием «НПП ПРОТОН», в которую входят:
- лазер СО2 для зачистки изоляции проводов
- машинка для подкрутки и снятия изоляции
- модуль флюсования
- модуль лужения.
Данная линия позволяет производить подготовку концов проводов к монтажу (пайке), а именно:
- с помощью лазера делаем рез на изоляции на заданной длине,
- с помощью машинки снимаем отрезанный кусочек изоляции с конца провода, также на этой машинке мы можем скручивать несколько проводов вместе (при необходимости);
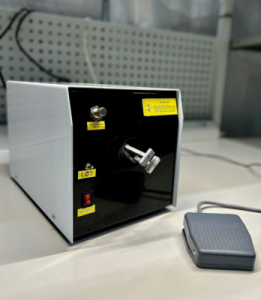
- производим флюсование;
- облуживаем зачищенные концы провода припоем в модуле лужения.
3. После подготовки раскладываем провода на плазе и заделываем концы проводов в картонки, которые имитируют количество и расположение контактов в данном конкретном разъеме. Для данных целей будем использовать станок ЧПУ производства «НПП ПРОТОН» для раскладки проводов на плазе. С помощью станка раскладываются все провода, которые входят в состав жгута, формируется тело жгута, формируются его плечи (ответвления), а также каждый конец провода заделывается в оснастку, которая имитирует разъем в части количества и расположения контактов, что облегчает труд электромонтажника при распайке проводов в разъемы, а также сводит к минимуму ошибки, допускаемые при распайке разъемов (не тот провод не в тот контакт).
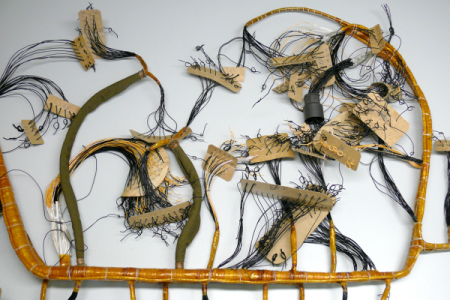
Станок работает по трем основным осям – X, Y, Z. В его память записывается цифровой двойник эталонного жгута, т.е. оператор выбирает тот жгут, который необходим ему по заданию и станок самостоятельно раскладывает провода на плазе. Станок может автономно работать в круглосуточном режиме, тем самым подготавливая жгуты на следующую рабочую смену.
Таким решением мы в несколько раз ускоряем процесс подготовки проводов к монтажу, раскладываем провода в автоматическом режиме на плазе и освобождаем электромонтажника от прозвонки проводов, т.е. экономим его время при распайке разъемов, а также уходим от такой проблемы, как человеческий фактор, так как жгут будет собран согласно КД и электрической схеме жгута.
Еще один участок, для которого мы закупили новинки – участок маркировки.
Согласно КД все разъемы, бирки, маркировочные трубки необходимо маркировать перед установкой на кабельный жгут, при этом надписи должны быть читаемы, не стираться, не выцветать, не исчезать при воздействии бензина, спирта и т.п. материалов, не растрескиваться со временем. На данный момент это в основном делается вручную, либо на станках, которые были изготовлены в прошлом веке. После гравировки материала место гравирования заливается краской. На данный момент, в связи с возросшим объемом производства, электромонтажники проводят целую смену за станком для гравирования. Помимо этого они размечают вручную место для гравировки и подписывают на бумаге обозначение, которое необходимо выгравировать. Да, сейчас вы можете сказать, что есть лазеры, с помощью которых наносится обозначение на трубки, либо термотрансферные принтеры. Но заказчик бросил нам вызов – им необходимо было маркировать такой материал, как полиамид.
Врагу не сдается наш гордый варяг и мы нашли решение и для этой задачки, и приобрели два станка.
Один из них - Ультрафиолетовый лазер. Маркирует всё – пластинки и разъемы из полиамида, наносит маркировку на различные виды трубок (305 ТВ-40/ТУТ/ТТК), картон, металлические бирки. При этом ничего не прожигает, а надписи читаемы. Но самое главное, что надписи не стираются и не выгорают, не исчезают со временем.
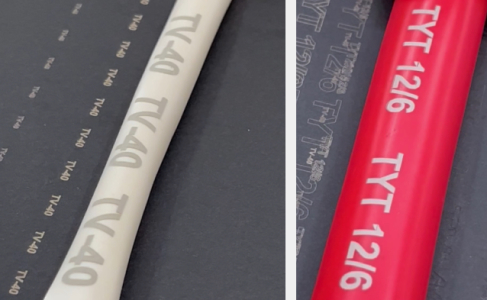
Еще одна из фишек нашего лазера – мы можем с помощью конвейера (идет в комплектации с лазером) и машинного зрения делать маркировку сразу нескольких разъемов, то есть раскладываем на конвейер несколько разъемов, конвейер движется и как только разъем попадает в поле машинного зрения и работы лазера, то на него наносится маркировка.
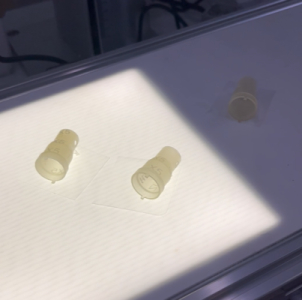
Второй - Лазер для маркировки и гравировки металлических разъемов. Мы протестили все виды разъемов - РМ, РМД, РМДТ, РС, РРС3, МР, СНЦ и т.д. На любом из этих разъемов результат нас удовлетворил, как и заказчика. В зависимости от требований КД, Вы можете либо промаркировать разъем, либо сделать на нем гравировку.
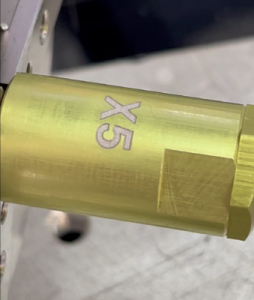
Теперь электромонтажник в любой момент может подойти к любому из лазеров и, нажав пару кнопок, получить готовый результат.
Заготовительный участок + склад МПКИ + склад готовой продукции
Как мы знаем, при изготовлении жгутов их приходится перемещать с одного участка на другой, а также ходить на склад материалов и ПКИ за комплектующими, что занимает время электромонтажника. Именно поэтому, мы подумали и решили – а почему бы не внедрить на производство VGA-тележки? Роботизированные тележки в количестве 10 штук, курсируют по цеху в автоматическом режиме, согласно программному заданию, при необходимости вызываются электромонтажником, тем самым освобождая его для выполнения более важных задач, чем перемещение между участками.
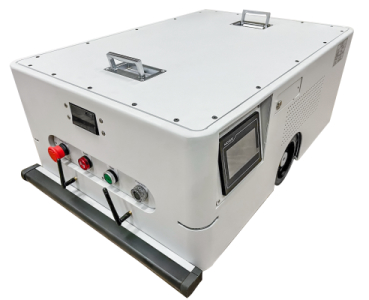
Тележка служит для доставки материалов, покупных комплектующих, комплектующих собственного производства со склада на участок, а также для доставки тела жгута с заготовительного участка на участок электромонтажа, с участка электромонтажа на другие участки цеха для дальнейшей сборки и для сбора готовых кабельных жгутов и их доставки на склад готовой продукции.
Участок электромонтажа
После сборки тела жгута делается электромонтаж (пайка разъемов). Качественный и быстрый электромонтаж возможен только при наличии надежных инструментов, оборудования, приспособлений, но как часто это бывает закупаются самые дешевые инструменты и оборудование, которые очень быстро выходят из строя, особенно если учитывать нынешние темпы производства. Но, помимо этого, нужно позаботиться и о здоровье рабочего персонала.
И поэтому мы предложили следующее оборудование:
- паяльные станции Альфа;
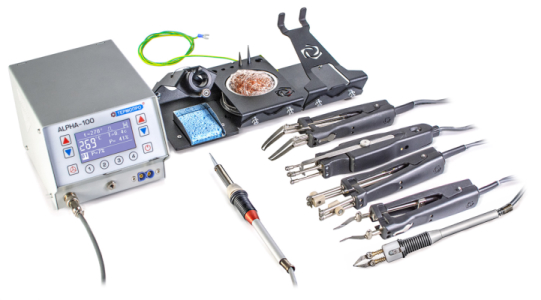
Альфа 102-ИТ - цифровая многофункциональная паяльная станция, к которой помимо паяльника можно подключать до пяти различных термоинструментов.
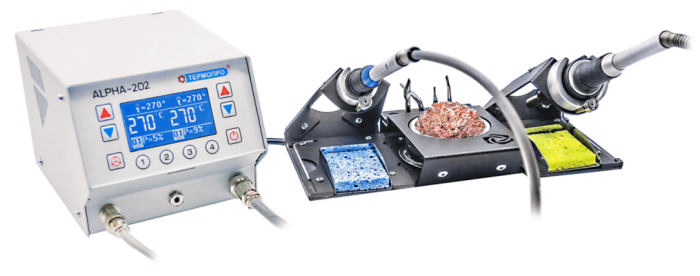
Альфа 202 с паяльниками мощностью 100 и 200 Вт – цифровая паяльная станция, на первом канале которой работает испытанный временем и модернизированный паяльник α-100, а на втором канале подключен новый паяльник α-200. Предусматривается возможность включения/выключения нагрева паяльных инструментов в любом сочетании.
- паяльные станции AiXun (аналог JBC);
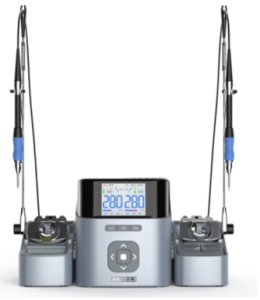
- сменные жала для всех видов работ к обоим видам паяльных станций;
- обжигалки одно- и двух петельные для снятия изоляции;
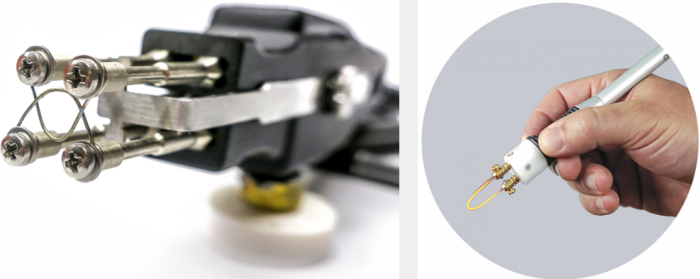
- струбцина/тиски для крепления разъемов при пайке;
- дымоуловители для отвода воздуха с вредными примесями с рабочего места.
Всё это оборудование уже опробовано в производстве и доказало свою надежность, а в случае поломки - ремонтопригодность.
Следующий интересный участок - Участок раскладки и лентообмотки жгутов
После электромонтажа (в некоторых случаях данная операция делается до электромонтажа) необходимо разложить жгут, расправить провода, уложить плечи жгута, подготовить жгут к обмотке одной или несколькими видами лент и обмотать жгут лентой. Либо как это делалось ранее и делается по сей день – протянуть жгут и его плечи в трубки 305 ТВ-40/305 ТВ-50/305 ТВ-60 и наложить бандажи на место стыка трубок. Но все это занимает много времени – бывает, что провода в трубку сложно протянуть или в процессе протяжки механически повредили трубку, а это значит, что трубка снимается и вся операция начинается заново. А сколько времени уходит на ручное бандажирование тела жгута, особенно если по КД заложено несколько видов лент, которые наматываются друг на друга.
Наше предложение на эту проблему:
Восьмиметровый плаз с перфорацией для раскладки и лентообмотки жгутов. На плазе при помощи штырьков раскладываем и закрепляем жгут, его плечи (ответвления), расправляем провода, укладываем плечи жгута. Так как плаз восьмиметровый, то на нем одновременно могут работать несколько человек (если жгуты в длину до 4 м). Далее на нем же - поднимаем по штырькам жгут на высоту примерно 150-200 мм от плаза и с помощью ручной машинки для бандажирования делаем бандаж из изоленты или ленты фторопластовой на теле жгута, его ответвлениях и бандажируем места стыка плеч и основного тела жгута. При этом, если штырь в процессе обмотки нам мешает, мы можем его достать, а потом вернуть на место или наоборот – где-то еще дополнительно его установить при необходимости. Ручная машинка для бандажирования может подвешиваться к несущей конструкции, тем самым мы облегчаем ее вес, и рука электромонтажника не будет уставать, а также можем регулировать скорость обмотки, что позволит нам видеть и чувствовать процесс обмотки.
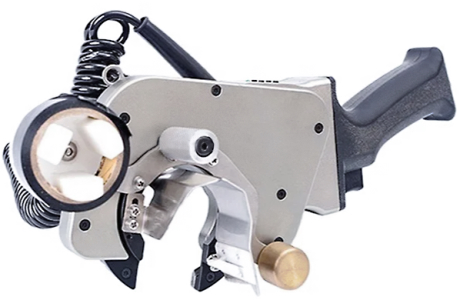
А теперь самый завораживающий участок - Участок оплетения. Приятно же смотреть как работают другие? В нашем случае это станок для оплетения.
Согласно КД и технологии сборки кабельных узлов, после бандажирования жгут и его плечи протягивают в готовую плетенку. На этот этапе мы должны подготовить плетенку к продеванию в неё тела жгута, то есть растянуть до необходимого диаметра, так как плетенка приходит, намотанная на бухты в плоском виде. После растяжки в неё продевается тело жгута, и также как в ситуации с трубкой – то тяжело протянуть, то плетенку повредили, а значит снимаем ее и начинаем операцию сначала. А после накладываем металлический бандаж на места стыка нескольких видов плетенки. Если жгут трудоемкий и сложный по исполнению, то на данную операцию может уйти полсмены и больше.
Но мы не сдаемся и предложили такой вариант – станки для оплетения жгутов проволокой на 24 и 36 катушек. Тем самым этими двумя станками мы можем делать любой типоразмер плетенки, задействуя либо все катушки, либо только их часть. Оператору только остается установить жгут в месте схождения всех проволочек и нажать кнопку «Старт». Если жгут длинный, то он в автоматическом режиме наматывается на барабан станка.
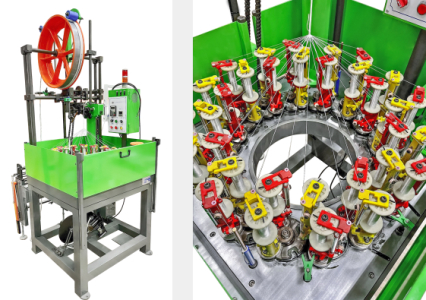
Но самое интересное в этих станках – это то, что мы нашли не полностью подходящие станки для оплетения под требуемую технологию. Да, мы могли их просто закупить, поставить заказчику и сказать – это лучшее, что есть на рынке. Но тогда это будем не мы, и поэтому было принято решение об их доработке, а именно – вырезать отверстие в площадке, на которую крепятся катушки, чтобы мы могли оплетать любой жгут, не задумываясь о его длине. Еще хотелось бы отметить такой момент – наш станок работает по-настоящему тихо, то есть можно стоять рядом со станком и разговаривать как обычно, не повышая голос. А все это благодаря конструкции станка, его шестерни работают в емкости с маслом, что и создает эффект малошумности. Остается только наслаждаться процессом.
Станок может работать не только с медной луженой проволокой, но и с медной посеребренной проволокой, моноволоконными нитями.
Следующий участок для представления – Участок герметизации и полимеризации.
После оплетения есть еще один немаловажный этап в изготовлении кабеля – это герметизация. Все разъемы после распайки герметизируются, в зависимости от технологии производства – компаундами, герметиками, пеногерметиками. Также при склейке различных материалов и на резьбовые соединения могут наноситься различные клея. Но и тут не бывает без проблем. Основная из них – компоненты на многих производствах смешиваются вручную. При таком смешивании очень часто бывают неоднородности и руками большой объем не смешаешь, а иногда для одной операции по герметизации необходимо не менее 1 кг материала. Либо предприятия используют самодельные миксеры, но и они не дают 100% результат при смешивании. И очень часто встает вопрос о дозировании приготовленного материала.
На что мы предложили для смешивания всех компонентов использовать планетарный миксер, а для дозированной заливки под давлением - экструдер и дозатор. Наши миксеры служат верой и правдой уже не на одном предприятии, в том числе и в отрасли ВПК.
Как мы с Вами знаем после заливки герметика/клея его необходимо полимеризовать. Есть такие материалы, у которых время полимеризации составляет 72 часа. Но на данный момент у нашей отрасли нет столько времени на ожидание. Поэтому мы предложили использовать печи для полимеризации материалов, тем самым сократив время сушки до нескольких часов. Но стоит отметить, что такой вариант подходит не для всех материалов.
И завершающий участок – участок электроконтроля.
После операции электромонтажа, обмотки лентой, оплетения и полимеризации необходима проверка электрических параметров жгута. На данный момент у многих предприятий эта операция проводится тремя разными приборами, что не удобно и не экономит наше драгоценное время.
Поэтому мы обратились к нашим коллегам и друзьям, с которыми совместно провели работу и ребята изготовили для нас тестер жгутов. Тестер проводит проверку правильности распайки согласно электрической схемы жгута, проверку сопротивления изоляции и проверку электрической прочности изоляции (пробой) по заранее прописанной программе. Оператору только остается подключить жгут к тестеру, выбрать программу и всего за пару минут получить готовый результат, затем снять жгут и распечатать протокол испытаний. И мы опять выиграли время при проверке кабельных жгутов.
Подведем итог – работа была сложной и в тоже время увлекательной. Было изучено много КД, ГОСТов, ОСТов, ТУ на материалы. Были применены знания и опыт с предыдущих проектов, проведены встречи с конструкторами, технологами и электромонтажниками, которые работают в отрасли ВПК, выдвинуто много разных идей, некоторые из них были реализованы в нашем проекте. Самая главная задача, которую мы выполнили – это сократили время изготовления жгутов, а также спроектировали планировку цеха и участков так, чтобы кабельные жгуты можно было собирать как в ручном, так и в полуавтоматическом, и в автоматическом режимах.
Думаете это всё? А вот и ошибаетесь. Сейчас расскажу Вам про вишенку на торте. Как известно отрасль ВПК очень консервативна, особенно это касается литерных изделий, которые собираются годами по одной и той же КД, технологии, одними и теми же материалами. Но наша компания не из тех, кто просто купил станки, поставил их заказчику, настроил их работу и помахал всем ручкой на прощание. Мы взялись за работу серьезно – разобрали КД на изготовление жгутов, поняли, что в жгутах есть материалы, которые не играют особой роли при изготовлении, разобрали все узкие места при изготовлении и предложили свои варианты решения, то есть начали работать с конструкторами и вносить изменения в КД (литерное!!!).
Первое изменение, которое мы предложили – заменить трубки 305 ТВ-40, 305 ТВ-50, ленту кремнеземную марки КЛ, ленту склеивающую марки ЛТ на электроизоляционную термостойкую самослипающуюся ленту ЛЭТСАР марки «К» тип «Г». Тем самым электромонтажнику не нужно протягивать жгут в трубку, накладывать бандажи на места соединения трубок, а также мотать вручную несколько слоев различных лент. ЛЭТСАР выдерживает температуру от -50°С до +250°С, кратковременно +300°С, тип «Г» полностью слипается за 3 часа при температуре 150°С. Цех одобрил наше нововведение, но было одно «но». Лента при укладке на изделии тяжело протягивается через отверстия, трубки и т.п., прилипает к внутренним стенкам. Тогда мы предложили сверху дополнительно обматывать жгут липкой лентой фторопластовой. Лента дает нам дополнительную защиту ЛЭТСАРа и необходимое скольжение при протяжке. При применении этих двух лент мы получаем уменьшение трудоемкости при изготовлении жгута, более легкий по весу жгут и сохраняем его гибкость. Более подробно опыт применения ленты ЛЭТСАР при изготовлении кабельных жгутов мы ранее описали в статье в журнале Электроника НТБ 2024 №1.
Второе изменение, которое было нами предложено – заменить три вида материала (виксинт ПК-68-1, компаунд ЭЗК-6, герметик ВГО-1) по заливке разъемов на один. Это самое узкое место в технологии изготовления жгутов относительно скорости процесса, так как этот этап может занимать до 72 часов (заливка + сушка). Мы долго искали и нашли материал, которым можно заливать разъемы. Он однокомпонентный, время полимеризации примерно 2-3 часа (в зависимости от объема), материал обладает высокой адгезией не только к металлу, но и фторопластовой изоляции проводов, не впитывает в себя влагу, не охрупчивается при заморозке. Материал состоит из гранул, расплавляется в печке при температуре 180-200°С, заливается в горячем виде в разъем и остается полимеризоваться при комнатной температуре в течение 2-3 часов. Материал был испытан нами после заливки в климатической камере при температуре -60°С. Никаких изменений в структуре материала не произошло.
Заказчик ещё не принял окончательное решение по внедрению данного материала, но его испытания показали отличный результат. Если все пойдет по плану, то мы заменим три материала на один и ускорим процесс герметизации и полимеризации как минимум в 10 раз. Хотелось бы отметить, что на данный момент мы ведем переговоры с рядом российских предприятий о локализации производства данного материала у нас в России.
И напоследок хочу сказать – не бойтесь перемен, даже если они происходят в такой консервативной отрасли как ВПК, боритесь за свои производства, не бойтесь менять КД, ведь сейчас столько новинок в области оборудования и материалов, которые в несколько раз превосходят по своим характеристикам оборудование и материалы прошлых лет.
Статья размещена в журнале "ЭЛЕКТРОНИКА: НТБ" №3 2024 г.